What is it about?
This article addresses how to create an efficient production plan for a manufacturing system that includes a process for recovering and remanufacturing used products. The focus is on developing a strategy to balance production and remanufacturing efforts to meet demand while considering environmental regulations and raw material shortages. By using advanced mathematical techniques, the article provides a way to estimate future production needs and reduce costs. The approach helps managers plan better by offering scenarios that incorporate the reuse of returned products, ensuring more sustainable and cost-effective operations. A simple example demonstrates how these ideas can be applied in practice.
Featured Image
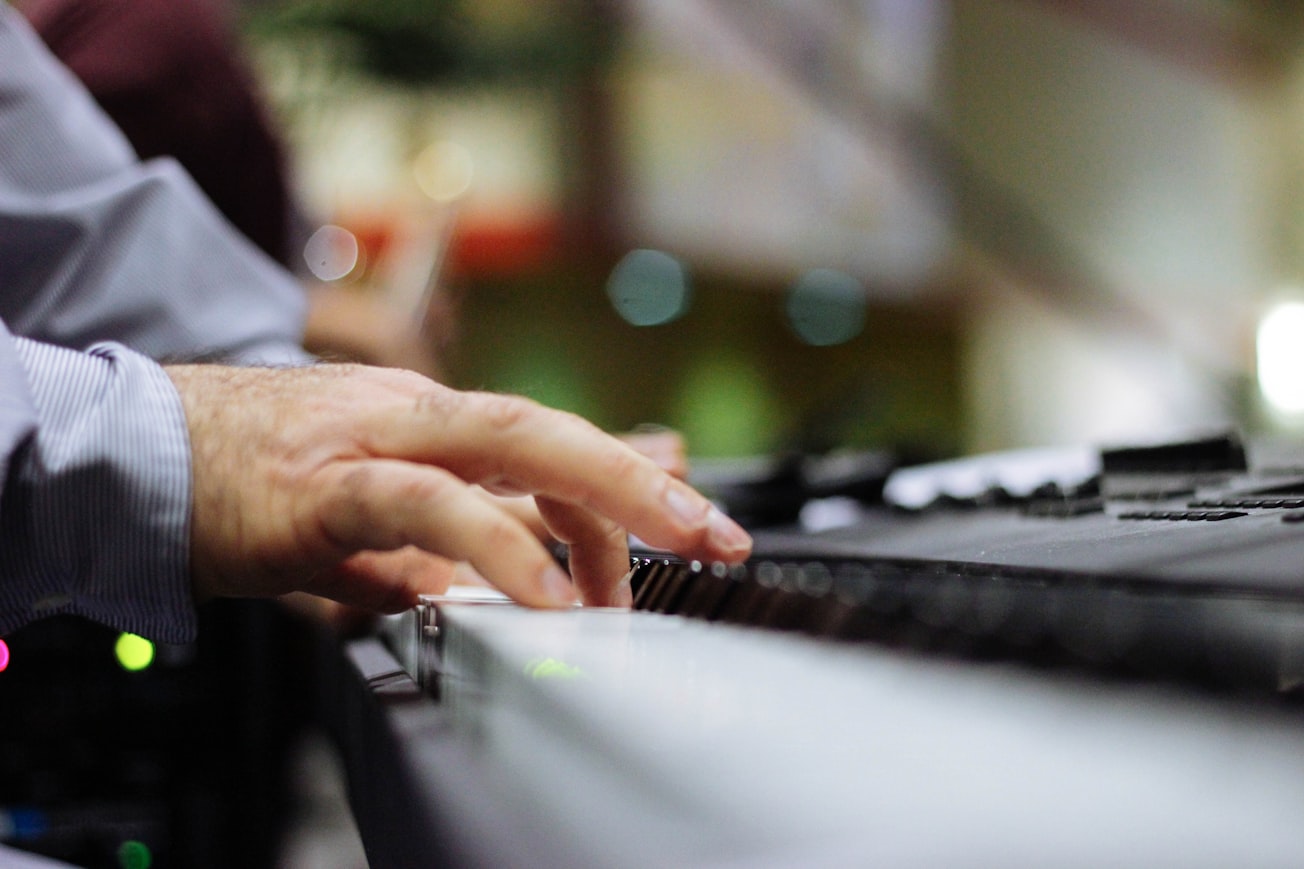
Photo by Gabriel Barletta on Unsplash
Why is it important?
Creating an efficient production plan for a manufacturing system with a recovery process is important for several reasons: (1) Environmental Sustainability: Remanufacturing used products reduces waste and minimizes the environmental impact by promoting the reuse and recycling of materials. This aligns with increasing global emphasis on sustainability and environmental responsibility. (2) Resource Optimization: With raw material shortages becoming more common, efficient recovery and reuse of materials help in conserving natural resources. This ensures that manufacturing processes can continue smoothly even when raw materials are scarce. (3) Cost Reduction: Remanufacturing can lower production costs by reusing materials and components from returned products. This can lead to significant savings and increased profitability for businesses. (4) Compliance with Legislation: Many industries face specific regulations regarding the return and recycling of used products. An optimal production plan that includes remanufacturing helps companies comply with these laws, avoiding potential fines and legal issues. (5) Market Demand: Fluctuations in market demand can be better managed with a flexible production plan that includes remanufacturing. It allows companies to adapt more quickly to changes in demand, maintaining customer satisfaction and market competitiveness. (6) Strategic Planning: The proposed approach provides managers with valuable scenarios to evaluate future opportunities, such as potential cost reductions and efficiency improvements. This strategic insight is crucial for long-term business planning and growth. (7) Innovation and Competitive Advantage: Incorporating remanufacturing into production processes can spur innovation in product design and manufacturing techniques. Companies that effectively implement such strategies can gain a competitive edge in the market by offering sustainable and cost-effective products.
Perspectives
here are some additional perspectives on the importance and implications of creating an optimal production plan for a manufacturing system with a recovery process: (1) Circular Economy: This approach aligns with the principles of the circular economy, which aims to minimize waste and make the most of resources. By integrating remanufacturing into production plans, companies contribute to a more sustainable economic model where products and materials are kept in use for as long as possible. (2) Consumer Expectations: As consumers become more environmentally conscious, companies that adopt sustainable practices, such as remanufacturing, can enhance their brand reputation and appeal to eco-friendly consumers. This can lead to increased customer loyalty and market share. (3) Technological Advancement: Developing sophisticated models for production planning that include remanufacturing encourages technological innovation. This can lead to advancements in areas such as inventory management, demand forecasting, and supply chain optimization. (4) Risk Management: Incorporating remanufacturing into production planning helps mitigate risks associated with supply chain disruptions. By having a recovery process in place, companies are less vulnerable to fluctuations in raw material availability and can maintain steady production levels. (5) Global Impact: On a broader scale, widespread adoption of such production plans can significantly reduce the global demand for raw materials and decrease the environmental footprint of manufacturing industries. This collective impact can contribute to global sustainability goals and climate change mitigation efforts. (6) Economic Benefits: Beyond cost savings, remanufacturing can create new business opportunities and revenue streams. For instance, companies can develop new markets for remanufactured products or offer services related to product returns and refurbishing. (7) Collaboration and Innovation Ecosystem: Implementing these strategies often requires collaboration across different sectors, including suppliers, manufacturers, and recycling companies. This fosters an innovation ecosystem where best practices and technologies are shared and developed collaboratively, benefiting the entire industry.
Dr. HDR. Frederic ANDRES, IEEE Senior Member, IEEE CertifAIEd Authorized Lead Assessor (Affective Computing)
National Institute of Informatics
Read the Original
This page is a summary of: Optimal production plan for a manufacturing system with associated recovery process, July 2016, Institute of Electrical & Electronics Engineers (IEEE),
DOI: 10.1109/acc.2016.7526692.
You can read the full text:
Contributors
The following have contributed to this page